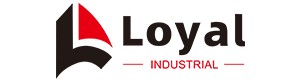
- Shandong Loyal Industrial Co.,Ltd.
- Macaroni Production Machine Instant Noodle Machine Biscuit Making Machine

Home> Company News> Discover The Secret To Perfect animal pellet maker: animal pellet maker Recipes

Discover The Secret To Perfect animal pellet maker: animal pellet maker Recipes
2024-09-26 09:40:47Brief Overview of the Animal Feed Industry and the Importance of Pelletization
The animal feed industry stands as a cornerstone of modern agriculture, fueling the growth and productivity of livestock worldwide. From poultry farms to cattle ranches and aquaculture facilities, animals rely on a steady supply of nutritious feed to thrive. As the global population continues to rise, so does the demand for animal protein, putting pressure on the feed industry to produce more efficiently and sustainably.
Within this context, pelletization has emerged as a crucial step in the production of animal feed. Pellets are formed by compressing and extruding feed ingredients into small, uniform particles, offering several advantages over traditional feed forms such as meal or mash.
Firstly, pelletization improves the digestibility and palatability of feed, making it more appealing to animals and enhancing nutrient absorption. This leads to better growth rates and overall health, translating into increased productivity for farmers and ranchers.
Moreover, pellets are highly convenient to handle and store. Their compact shape reduces dust and spillage, making feed distribution more efficient and hygienic. This is particularly important in large-scale operations where feed management can be a significant challenge.
From an economic perspective, pelletization can also contribute to cost savings. By optimizing the use of feed ingredients and reducing waste, producers can maximize the value of their raw materials. Additionally, the consistent quality of pellets ensures that animals receive a balanced diet, reducing the need for costly supplements or veterinary interventions.
As the animal feed industry continues to evolve, the importance of pelletization is only set to grow. This is where fully automated animal pellet makers come into play, offering a revolutionary solution for streamlining production with high efficiency and energy savings. By harnessing the latest technologies in automation and precision control, these machines are transforming the way animal feed is produced, paving the way for a more sustainable and profitable future.
Highlighting the Need for Efficiency and Energy Savings in Modern Feed Production
In today's fast-paced and resource-constrained world, the animal feed industry faces unprecedented challenges. The demand for efficient and sustainable production methods is paramount, as producers strive to meet the growing needs of a global population while minimizing their environmental footprint.
Efficiency and energy savings are two critical factors that have emerged as central to modern feed production. The process of manufacturing animal feed is inherently energy-intensive, from grinding and mixing raw materials to drying and pelletizing the final product. As such, there is a pressing need for innovative technologies that can streamline these operations, reducing waste and maximizing output.
Fully automated animal pellet makers are at the forefront of this drive for efficiency and energy savings. These advanced machines utilize sophisticated automation systems to optimize every step of the pelletization process, from precise ingredient metering and mixing to continuous pellet extrusion and cutting. By automating these tasks, producers can eliminate human error, reduce downtime, and achieve consistent product quality.
Moreover, fully automated pellet makers often incorporate energy-efficient features such as variable speed drives, high-efficiency motors, and insulation to minimize heat loss. These design elements help to reduce the overall energy consumption of the machine, translating into significant cost savings for producers.
As the global focus on sustainability continues to intensify, the need for efficient and energy-saving production methods in the animal feed industry becomes even more urgent. By investing in fully automated animal pellet makers, producers can demonstrate their commitment to environmental responsibility while positioning themselves for long-term success in an increasingly competitive market.
Key Components and Their Roles in the Production Process of a Fully Automated Animal Pellet Maker
The fully automated animal pellet maker is a complex system comprising several key components, each playing a crucial role in the efficient and effective production of animal feed pellets. Understanding these components and their functions is essential for maximizing the performance of the machine and ensuring consistent product quality.
Feed Preparation System: This component is responsible for preparing the raw materials for pelletization. It typically includes a mixer that blends various ingredients in precise proportions, ensuring that each batch of feed meets the required nutritional specifications. The mixer is designed to ensure thorough and uniform mixing, which is crucial for the quality of the final pellets.
Conditioning System |
Following mixing, the feed is passed through a conditioning system, which further prepares it for pelletization. This system typically includes a steam injector that adds moisture and heat to the feed, making it more pliable and easier to form into pellets. The conditioning process is critical for achieving high-quality pellets with good durability and digestibility. |
Pellet Mill |
The pellet mill is the heart of the fully automated animal pellet maker. It consists of a rotating die with numerous holes through which the conditioned feed is extruded under intense pressure. The die is typically made from hardened steel to withstand the high pressures and temperatures involved in the pelletization process. The rotating action of the die, combined with the force of the feed being pushed through the holes, results in the formation of solid pellets. |
Knife Cutter |
Once the pellets exit the die, they are cut to a uniform length by a knife cutter. This component ensures that the pellets are of a consistent size, which is important for ease of handling and feeding to animals. The knife cutter is designed to operate in sync with the pellet mill, ensuring a continuous and efficient cutting process. |
Cooling and Drying System |
After cutting, the pellets are typically passed through a cooling and drying system to remove excess moisture and stabilize their temperature. This step is crucial for preventing the pellets from sticking together or becoming moldy during storage. The cooling and drying system may use forced air or other methods to achieve the desired results. |
Control System |
The fully automated animal pellet maker is equipped with an advanced control system that monitors and adjusts the various process parameters in real-time. This system ensures that the machine operates at peak efficiency, producing high-quality pellets with minimal waste. The control system may include sensors that monitor factors such as feed flow rate, die temperature, and pellet quality, allowing for precise adjustments to be made as needed. |
High Efficiency in Animal Pellet Production with a Fully Automated Animal Pellet Maker
In the world of animal feed production, efficiency is key to maintaining profitability and meeting the demands of a growing global population. A fully automated animal pellet maker represents a significant leap forward in achieving this goal, streamlining the production process and maximizing output with minimal waste.
1.Automated Feed Handling: One of the primary benefits of a fully automated animal pellet maker lies in its ability to handle raw materials efficiently. By integrating automated feed handling systems, the machine can accurately measure and mix ingredients, reducing the risk of human error and ensuring consistent quality throughout the production cycle. This not only saves time but also minimizes the need for manual labor, freeing up resources for other tasks.
2.Continuous Production: Another key aspect of high efficiency in animal pellet production is the ability to operate continuously. A fully automated pellet maker is designed to run non-stop, with minimal downtime for maintenance or adjustments. This continuous production capability allows manufacturers to produce large quantities of pellets quickly, meeting the demands of the market without compromising on quality.
3.Optimized Pelletizing Process: The pelletizing process itself is highly optimized in a fully automated system. The conditioning and extrusion steps are precisely controlled, ensuring that the pellets are formed with the desired density, shape, and durability. This optimization reduces the need for reworking or discarding defective pellets, saving both time and resources.
4.Energy Efficiency: Energy savings are also a significant factor in the high efficiency of a fully automated animal pellet maker. Modern machines are designed to minimize energy consumption during operation, using advanced motors and drive systems that require less power to run. Additionally, the efficient handling of raw materials and continuous production capabilities reduce the overall energy footprint of the production process.
5.Data-Driven Monitoring and Control: A fully automated animal pellet maker is equipped with advanced data-driven monitoring and control systems. These systems continuously collect and analyze data on various process parameters, such as feed flow rate, die temperature, and pellet quality. Based on this data, the machine can automatically adjust its operating parameters to optimize performance and minimize waste. This level of precision and control is not possible with manual or semi-automated systems, making fully automated pellet makers the clear choice for high-efficiency production.
Energy Savings in Fully Automated Animal Pellet Makers
In the realm of industrial food machinery, energy efficiency is a paramount concern for manufacturers looking to reduce their operational costs and minimize their environmental impact. Fully automated animal pellet makers are no exception, offering significant energy savings that can translate into substantial long-term benefits.
Advanced Motor Technology |
At the heart of energy savings in fully automated animal pellet makers lies advanced motor technology. These machines utilize high-efficiency motors that require less power to operate compared to traditional motors. By reducing the energy consumption during the pelletizing process, manufacturers can see a noticeable decrease in their electricity bills. |
Optimized Process Control |
Another key factor contributing to energy savings is the optimized process control offered by fully automated systems. By precisely controlling various process parameters such as feed flow rate, die temperature, and pressure, the machine can operate at peak efficiency, minimizing energy waste. This level of precision is not achievable with manual or semi-automated systems, further underscoring the advantages of fully automated animal pellet makers. |
Efficient Heating and Cooling Systems |
Heating and cooling are critical steps in the pelletizing process, and fully automated animal pellet makers are designed to optimize these processes for maximum energy efficiency. Advanced heating elements and efficient cooling systems ensure that the required temperatures are achieved quickly and maintained consistently, reducing the need for excessive energy input. |
Idle Time Reduction |
Fully automated systems also help reduce idle time, which can consume significant amounts of energy if left unchecked. By continuously monitoring and adjusting the production process, these machines minimize downtime and ensure that production runs smoothly, reducing the overall energy footprint of the operation. |
Environmental Benefits |
Beyond the direct financial savings, the energy efficiency of fully automated animal pellet makers also brings significant environmental benefits. By reducing energy consumption, these machines contribute to a lower carbon footprint and help manufacturers meet their sustainability goals. |
Maintenance and Operational Considerations for Fully Automated Animal Pellet Makers
Operating a fully automated animal pellet maker with high efficiency and energy savings requires a keen eye on maintenance and operational considerations.
Regular Maintenance Schedules |
Regular maintenance is the cornerstone of maintaining the high efficiency and reliability of fully automated animal pellet makers. Establishing a comprehensive maintenance schedule that includes regular inspections, cleaning, and component replacements can significantly extend the lifespan of the machine. Manufacturers should ensure that maintenance tasks are carried out by trained personnel, who are familiar with the specific requirements of the machine. |
Quality Feed Material |
The quality of the feed material used in the pelletizing process has a direct impact on the operational efficiency of the machine. Using poor-quality or inconsistently sized feed can lead to blockages, wear and tear on components, and ultimately, reduced productivity. Manufacturers should ensure that the feed material meets the specified requirements, including moisture content, particle size, and consistency. |
Temperature and Moisture Control |
Accurate temperature and moisture control are essential for achieving optimal pellet quality and maintaining machine efficiency. Fluctuations in these parameters can affect the consistency of the pellets, as well as the wear and tear on the machine's components. Fully automated animal pellet makers are equipped with advanced systems that automatically adjust these parameters to ensure consistent results. However, manufacturers should still monitor these systems regularly to ensure they are functioning correctly. |
Operator Training |
Proper operator training is vital for ensuring efficient and safe operation of fully automated animal pellet makers. Operators should be thoroughly trained on the machine's operating procedures, including how to adjust settings, perform routine maintenance, and troubleshoot common issues. This not only improves productivity but also minimizes the risk of accidents and equipment damage. |
Reference
The following are five authoritative foreign literature websites in the field of Industrial food machinery:
1. Food Engineering Magazine
Website: https://www.foodengineeringmag.com/
2.Food Processing Magazine
Website: https://www.foodprocessing.com/
3.Journal of Food Engineering
Website:https://www.journals.elsevier.com/journal-of-food-engineering
4. Food Manufacturing Magazine
Website:https://www.foodmanufacturing.com/
5. International Journal of Food Science & Technology
Website:https://onlinelibrary.wiley.com/