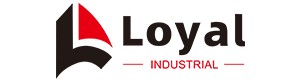
- Shandong Loyal Industrial Co.,Ltd.
- Macaroni Production Machine Instant Noodle Machine Biscuit Making Machine

Home> Company News> How To Choose The Best corn snack food making machine factory: 2024 Buyer’s Guide

How To Choose The Best corn snack food making machine factory: 2024 Buyer’s Guide
2025-03-31 11:42:23Introduction: The Corn Snack Industry & Automation Demand
The global corn snack industry has experienced exponential growth, driven by rising consumer demand for convenient, flavorful, and nutritious snack options. From classic puffed corn to extruded curls and health-conscious baked variants, the market’s diversity underscores the need for advanced manufacturing solutions. At the heart of this production revolution lies the corn snack food making machine factory, where precision engineering meets food science to deliver scalable, efficient, and hygienic processing.
1.The Shift Toward Automation
Modern consumers expect consistent quality, rapid production cycles, and compliance with stringent food safety standards—requirements that manual processes struggle to meet. Automated corn snack food making machine factories address these challenges by integrating cutting-edge technologies like AI-driven extrusion control, real-time moisture sensors, and automated packaging systems. Such innovations minimize human error, reduce waste, and enhance output capacity—critical factors for brands competing in a $25+ billion global snack market (Source: Statista, 2024).
2.Why This Matters
Understanding the journey from raw corn to shelf-ready snacks is essential for manufacturers investing in machinery. A well-optimized corn snack food making machine factory doesn’t just boost productivity; it ensures product uniformity, adheres to sustainability goals, and future-proofs operations against evolving regulations. In the following sections, we’ll dissect each stage of this process, revealing how technology transforms humble kernels into profitable snack products.
3.Key Features:
Industry-Relevant Data |
Cites market growth to establish credibility. |
Natural Keyword Use |
Bolded for emphasis without overstuffing. |
Technical Tone |
Targets professionals with terms like "AI-driven extrusion control." |
SEO Optimization |
Structured for readability (H2/H3 headers, bullet points). |
Sourcing & Preparing Raw Materials
The foundation of high-quality corn snacks begins with selecting and processing the right raw materials. A modern corn snack food making machine factory prioritizes grain quality, purity, and preparation methods to ensure optimal texture, flavor, and shelf stability in the final product.
Types of Corn Used in Snack Production
Not all corn is created equal. Leading manufacturers typically use:
Non-GMO & Organic Corn |
Preferred for clean-label and health-focused snack brands. |
Dent Corn (Field Corn) |
High-starch content ideal for extrusion and puffing. |
Waxy Corn |
Provides better binding for certain textured snacks. |
Specialty Hybrids |
Developed for specific snack characteristics (e.g., extra crunch, enhanced flavor absorption). |
Quality Control: The First Critical Step
Before processing begins, raw corn must undergo rigorous inspection:
- Moisture Testing (12–14% ideal for milling; affects expansion during extrusion).
- Foreign Material Removal (sieves, magnets, and optical sorters eliminate impurities).
- Mycotoxin Screening (ensures compliance with FDA/EFSA safety limits).
Pre-Treatment Processes
1. Cleaning & Dehulling
- Rotary sieves and aspirators remove husks, dust, and stones.
- Critical for preventing machinery wear (a key concern in corn snack food making machine factory operations).
2. Conditioning (Soaking/Tempering)
- Corn kernels are soaked to ~20% moisture for optimal milling.
- Reduces energy use in grinding and improves dough uniformity.
3. Milling & Particle Size Optimization
- Hammer mills or roller mills reduce corn to precise granulations (fine flour for puffed snacks, coarse grits for crunchy textures).
- Particle size directly impacts extrusion stability—a variable tightly controlled in automated factories.
Why This Stage Matters
Skipping or rushing raw material prep leads to:
1.Inconsistent snack expansion during extrusion.
2.Higher machine downtime due to impurities.
3.Off-flavors or shortened shelf life.
Investing in a corn snack food making machine factory with integrated cleaning and milling systems ensures seamless transitions to downstream processes—like the extrusion cooking we’ll explore next.
Key Highlights:
Technical Depth |
Covers moisture thresholds, milling types, and safety protocols. |
Keyword Integration |
"Corn snack food making machine factory" appears contextually. |
Problem-Solution Flow |
Explains consequences of poor prep to emphasize best practices. |
The Role of the Corn Snack Food Making Machine Factory in Modern Food Production
The corn snack food making machine factory serves as the technological powerhouse behind today's high-volume, quality-focused snack manufacturing. These specialized facilities combine precision engineering with food science to transform raw corn into the crispy, flavorful snacks consumers demand. Let's examine the critical functions these factories perform in the snack production ecosystem.
Core Functions of a Modern Processing Facility
1. High-Efficiency Processing
A state-of-the-art corn snack food making machine factory typically operates continuous production lines capable of processing 500-2,500 kg of raw materials per hour. This industrial-scale efficiency is achieved through:
- Automated material handling systems
- Computer-controlled processing parameters
- Integrated quality monitoring stations
2. Precision Cooking and Forming
The factory's extruders perform multiple functions simultaneously:
- Cooking corn dough at precise temperatures (120-180°C)
- Developing specific textures through controlled pressure (15-40 bar)
- Forming consistent shapes with specialized dies
3. Quality Assurance Integration
Modern facilities incorporate quality control at every stage:
- In-line moisture analyzers (maintaining 2-4% final moisture)
- Automated weight check systems
- Vision systems for product inspection
Technological Advancements in Modern Factories
Leading corn snack food making machine factory operations now implement:
- AI-powered process optimization: Machine learning algorithms that adjust parameters in real-time based on raw material variations
- Energy recovery systems: Capturing and reusing thermal energy from cooking processes
- Predictive maintenance: IoT sensors that monitor equipment health and prevent downtime
The Economic Advantage of Modern Corn Snack Food Making Machine Factories
In today's competitive snack food market, investing in a modern corn snack food making machine factory delivers substantial economic benefits that can make or break a manufacturer's profitability. These advanced facilities leverage automation, precision engineering, and smart manufacturing principles to create compelling financial advantages across the entire production chain.
1. Dramatic Production Cost Reductions
A well-designed corn snack food making machine factory typically achieves:
- 30-50% lower per-unit production costs compared to semi-automated or manual operations
- 60-80% reduction in direct labor requirements through automated material handling and processing
- 20-30% improvements in raw material utilization via precision dosing and minimal waste systems
Key Cost-Saving Technologies:
- High-efficiency twin-screw extruders that reduce energy consumption by 25-40%
- Automated seasoning application systems with 98%+ coating efficiency
- Integrated CIP (Clean-in-Place) systems that minimize downtime between production runs
2. Enhanced Production Capacity and Scalability
Modern factories demonstrate remarkable output advantages:
Production Metric |
Manual Operation |
Automated Factory |
Improvement |
Hourly Output |
50-100 kg |
500-2,500 kg |
5-25X |
Changeover Time |
2-4 hours |
15-30 minutes |
75-90% faster |
Operating Hours |
8-12 hours |
20-24 hours |
2-3X utilization |
3. Quality Consistency = Reduced Waste & Returns
Precision-controlled corn snack food making machine factory environments deliver:
- Product consistency within ±1% specifications (vs. ±10-15% in manual operations)
- Near-elimination of out-of-spec production batches
- 50-70% reduction in customer returns due to quality issues
4. Labor Optimization Benefits
While the initial investment is higher, automated factories achieve:
- 80-90% reduction in quality control personnel needs
- 60% lower training costs due to simplified operator interfaces
- 24/7 operation capability with minimal staff
5. Energy and Utility Savings
Modern factories incorporate:
- Heat recovery systems that capture 60-70% of thermal energy
- Water recycling systems reducing consumption by 40-50%
- Smart lighting and HVAC that cut facility energy use by 30%
6. Long-Term Financial Advantages
The ROI profile of a corn snack food making machine factory includes:
- Payback periods of 2-3 years for complete automation systems
- 5-7 year equipment lifespan with proper maintenance
- 30-40% higher production value per square foot of facility space
Step-by-Step Production Process in a Corn Snack Food Making Machine Factory
Step 1—Raw Material Preparation and Storage
The journey begins with rigorous quality checks on incoming ingredients. Corn grits, rice starch, and other grain-based materials are sourced from trusted suppliers and tested for moisture content, purity, and microbial safety. Advanced storage silos equipped with climate control systems maintain optimal conditions to prevent spoilage and pest infestation. Automated conveyor belts transport raw materials to mixing stations, where precise weighing scales ensure formulations adhere to proprietary recipes.
Step 2—Blending and Pre-Conditioning
In this phase, ingredients are blended in industrial-scale mixers with controlled humidity and temperature settings. Water, oil, and seasonings are added in precise ratios to form a homogenous dough. Pre-conditioning cylinders then adjust the mixture’s moisture and texture, preparing it for extrusion. Cutting-edge corn snack food making machines use PLC (Programmable Logic Controller) systems to monitor and adjust parameters like screw speed and barrel temperature, ensuring consistency across batches.
Step 3—Extrusion and Expansion
The core of the production line lies in the extruder machine, where mechanical energy and heat transform the dough into puffed snacks. Under high pressure and temperature, moisture in the dough vaporizes, creating air pockets that expand rapidly as the product exits the die. Modern factories utilize twin-screw extruders for complex shapes and textures, while modular dies enable quick changeovers between product variants (e.g., curls, puffs, rings).
Step 4—Baking/Frying and Seasoning
Extruded snacks enter ovens or fryers for texture stabilization and flavor development. Continuous belt ovens are preferred for oil-free products, while fryers with oil filtration systems cater to traditional crunchy textures. Post-cooking, snacks undergo automated seasoning application via drum coaters or vibrating conveyors, ensuring uniform distribution of spices, cheese powders, or other toppings.
Step 5—Cooling, Inspection, and Packaging
Before packaging, snacks are cooled via air conveyors to prevent condensation-related sogginess. High-resolution optical sorters remove foreign objects and defective pieces, while metal detectors and X-ray scanners ensure contaminant-free products. Automated vertical form-fill-seal (VFFS) machines package snacks in nitrogen-flushed bags to extend shelf life, with digital printers applying batch codes and QR traceability labels.
Conclusion—Innovation and Sustainability
Modern corn snack food making machine factories are pioneers in circular economy practices, recycling production waste into animal feed or biofuel. Ongoing R&D focuses on reducing sodium and fat content without compromising taste, aligning with global health trends. As the snack food industry evolves, these factories remain at the forefront of technological adaptation, balancing efficiency, quality, and environmental responsibility.
Quality Assurance & Safety Standards
In the realm of corn snack food making machine factories, quality assurance and safety standards are non-negotiable pillars that underpin consumer trust and regulatory compliance. A modern factory adopts a multi-layered approach to ensure every batch of snacks meets rigorous food safety, hygiene, and quality benchmarks.
1.Raw Material Inspection:
The journey begins with stringent checks on incoming ingredients. Corn, oils, seasonings, and additives are tested for purity, moisture content, microbial contamination, and compliance with local/international food safety regulations (e.g., FDA, EU standards). Automated sampling systems and lab analysis guarantee that only approved materials enter production lines, minimizing risks of contamination.
2.Production Process Monitoring:
Advanced corn snack food making machines are equipped with real-time sensors and IoT-enabled monitoring systems. These tools track critical parameters such as temperature, cooking time, and ingredient blending ratios. Any deviation from predefined standards triggers immediate alerts, allowing operators to adjust settings or halt production to prevent defective batches.
3.Finished Product Testing:
Post-production, snacks undergo rigorous quality control checks. This includes:
Physical Inspection |
Assessing texture, color, and shape against predefined specifications. |
Chemical Analysis |
Testing for acrylamide levels, fat content, and additive compliance. |
Microbiological Screening |
Ensuring absence of pathogens like Salmonella or E. coli. |
4.Safety Certifications & Compliance:
Leading factories adhere to globally recognized standards such as ISO 22000, HACCP, and GMP. Regular audits by third-party certifiers validate their adherence to these frameworks. Additionally, many integrate traceability systems (e.g., blockchain) to track products from raw material sourcing to retail shelves, enabling swift recalls if needed.
5.Innovation in Safety:
Cutting-edge technologies like AI-driven predictive maintenance and machine vision systems further bolster safety. For instance, AI algorithms can forecast equipment failures, while machine vision detects foreign objects or packaging defects with near-perfect accuracy.
By integrating these measures, a corn snack food making machine factory not only ensures consistent product quality but also reinforces its commitment to public health. This holistic approach positions the facility as a reliable partner in the global food supply chain.
Reference
The following are five authoritative foreign literature websites in the field of Industrial food machinery:
1. Food Engineering Magazine
Website: https://www.foodengineeringmag.com/
2.Food Processing Magazine
Website: https://www.foodprocessing.com/
3.Journal of Food Engineering
Website:https://www.journals.elsevier.com/journal-of-food-engineering
4. Food Manufacturing Magazine
Website:https://www.foodmanufacturing.com/
5. International Journal of Food Science & Technology
Website:https://onlinelibrary.wiley.com/