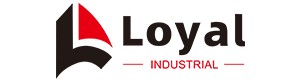
- Shandong Loyal Industrial Co.,Ltd.
- Macaroni Production Machine Instant Noodle Machine Biscuit Making Machine

Home> Processing> How To Maintain The Twin Screw Fish Feed Extruder?

How To Maintain The Twin Screw Fish Feed Extruder?
2021-04-28 15:18:29The feed production equipment has reasonable design, high degree of automation, and precise control of extrusion process parameters. The industrial floating fish food production line uses whole grains, soybean meal, fish meal, bone meal, meat meal, etc. as the main raw materials, and is extruded and granulated by an extruder at high temperature.
The feed production equipment has reasonable design, high degree of automation, and precise control of extrusion process parameters. The industrial floating fish food production line uses whole grains, soybean meal, fish meal, bone meal, meat meal, etc. as the main raw materials, and is extruded and granulated by an extruder at high temperature.
Daily maintenance of pet food making extruder:
1. The box bearing should be filled with lubricating grease in time, and all the lubricating grease should be replaced once after 500 hours of operation. (A proper amount of grease should be added to the new machine before operation, and the oil should be changed after 200 hours of operation.)
2. Grease should be added regularly to other bearing parts.
3. It is strictly forbidden to use hard objects and heavy hammers in the process of disassembly and assembly of vulnerable parts such as screws and screw sleeves. It is strictly forbidden to place heavy objects or stand people on the expansion cavity.
4. The puffed raw materials should be cleaned to prevent foreign objects such as metals from entering the machine and damaging the machine parts.
5. Check the quality of the extruder at any time and pay attention to the replacement of wearing parts.
6. Keep the area around the equipment clean.
7. When shutting down for a long time without using or replacing puffed materials, the materials in the puffing cavity should be removed to avoid agglomeration, mildew or cross-contamination between materials.
8. Since the wearing parts near the discharge port wear relatively quickly, and the wearing parts near the feed port are less worn, when replacing the wearing parts, they should be replaced sequentially from the discharge end, and it is not suitable to replace more than one at a time. Kind of parts.
Instructions for use of twin screws fish feed extruder machine:
Operating procedures:
1. Carefully check the screw and feeder for foreign matter before starting up, and clean it up.
2. Carefully check the position of the rotary cutter to ensure that the gap between each blade relative to the mold core plane is the same. It is not allowed to rely on the elasticity of the blade to tighten to eliminate the gap. This will not only damage the blades but also cause large wear and tear on the mold core, resulting in unnecessary Waste.
3. Carefully check all valve positions and pipelines for leaks.
4. After confirming that there is no abnormality, turn on the power supply. Turn on the temperature control and observe whether the meters are normal.
5. Check the condition of the raw materials and check whether they are evenly mixed.
6. Turn on the screw barrel heating valve and heat to the required temperature; turn on the main motor and observe whether the oil pump is working properly. Turn on the frequency converter to empty the remaining material in the screw, install the die body, and check the operation of the fan of the frequency conversion motor. Turn on the feed, turn on the feeder, add a little water to the screw, stop adding water after the material is discharged from the discharge port, observe the current, and adjust the production. During production, we must carefully observe the operation of the oil pump, the temperature of the motor, the temperature of the gearbox, etc., if any abnormality is found, stop the machine in time.
7. Observe current and adjust production. During production, we must carefully observe the operation of the oil pump, the temperature of the motor, and the temperature of the gearbox.
8 After the adjustment is normal, observe each link. And strictly prohibit hard objects from entering the machine. Observe the current, the raw materials, the finished product, and the oil circuit and the temperature of each area frequently. And always pay attention to the sound of equipment running, and learn to distinguish the size of the equipment bearing load.
9. After production, stop the feeder, run the main machine at low speed to cause the material to be basically discharged, stop the rotary cutter, and quickly disassemble the die body, turn on the main machine at a slow speed, empty the material, stop, and then the fan blows down the dust in the control cabinet And debris, keep it clean.
10. Turn off the main power supply, clean up the site and keep all tools properly.