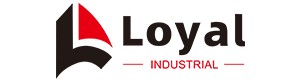
- Shandong Loyal Industrial Co.,Ltd.
- Macaroni Production Machine Instant Noodle Machine Biscuit Making Machine

Home> Company News> Everything you Need to Know About Fish Food Machine

Everything you Need to Know About Fish Food Machine
2024-04-18 15:41:31Introduction to Fish Food Machine Technology
Fish food machine technology represents a crucial aspect of the aquaculture industry, facilitating the production of high-quality feed for various aquatic species. These machines play a pivotal role in ensuring the nutritional needs of fish are met efficiently and effectively. Fish food machines encompass a range of sophisticated equipment designed to produce fish feed in various forms, including pellets, flakes, and extruded products.
The technology behind fish food machines has evolved significantly over the years, driven by the increasing demand for aquaculture products and advancements in manufacturing processes. Modern fish food machines incorporate state-of-the-art features such as precision control systems, automated production lines, and advanced materials to optimize feed production and meet the stringent quality standards of the industry.
Fish food machine technology encompasses a diverse array of equipment tailored to different production scales and feed formulations. From small-scale pelletizers suitable for artisanal fish farms to large-scale extruders capable of mass-producing specialized feed formulations, these machines cater to the diverse needs of aquaculture operations worldwide.
Components and Functions of Fish Food Machine
Fish food machines comprise several key components, each serving a specific function in the feed production process. These components work in harmony to transform raw ingredients into nutritious and digestible feed pellets or extrudates.
1. Extrusion Chamber: At the heart of many fish food machines lies the extrusion chamber, where raw ingredients are subjected to high temperature and pressure to undergo physical and chemical transformations. This process improves the digestibility and nutritional quality of the feed, ensuring optimal growth and health for the fish.
2. Feeding System: The feeding system of a fish food machine controls the flow of raw materials into the processing chamber. It consists of a hopper, conveyor belts, and feeders designed to deliver precise amounts of ingredients according to the desired feed formulation.
3. Mixing and Conditioning Section: Before extrusion or pelletization, the raw ingredients must be thoroughly mixed and conditioned to achieve uniformity and proper moisture content. This section of the fish food machine incorporates mixers, steamers, and conditioners to blend the ingredients and enhance their physical properties for efficient processing.
4. Die and Cutter Assembly: In pelletizing machines, the die and cutter assembly are critical components responsible for shaping the feed into uniform pellets of the desired size and shape. The die exerts pressure on the conditioned feed mixture, while the cutter precisely cuts the extruded pellets to the specified length.
5. Control and Monitoring System: Modern fish food machines are equipped with advanced control and monitoring systems that regulate various parameters such as temperature, pressure, and feed rate. These systems ensure consistent product quality and allow operators to adjust processing parameters in real-time for optimal performance.
Types of Fish Food Machines: Pelletizers, Extruders, Mixers
Fish food machines come in various types, each tailored to specific production needs and feed formulations. Among the most commonly used types are pelletizers, extruders, and mixers.
Pelletizers are a popular choice for producing fish feed in pellet form. These machines use a die and cutter assembly to shape the feed mixture into uniform pellets of predetermined sizes. Pelletizers offer versatility in pellet size and shape, making them suitable for a wide range of fish species and feeding preferences. They are particularly effective for producing sinking pellets, which are often preferred for certain fish species that feed near the bottom of the water column.
Extruders represent another essential type of fish food machine, particularly for producing floating fish feed. These machines utilize a high-temperature, high-pressure extrusion process to transform raw ingredients into expanded, floating feed pellets. Extruders offer advantages such as precise control over feed density and texture, as well as the ability to incorporate additives and supplements into the feed matrix effectively. Floating pellets produced by extruders are ideal for species that feed near the water's surface, such as tilapia and carp.
Mixers play a crucial role in the fish feed production process by ensuring the uniform distribution of ingredients and additives in the feed mixture. These machines blend raw materials, vitamins, minerals, and other additives to create a homogeneous feed mixture with consistent nutritional content. Mixers come in various designs, including horizontal paddle mixers, ribbon blenders, and vertical screw mixers, each suited to different production capacities and mixing requirements. Proper mixing is essential for achieving uniform feed quality and ensuring the optimal growth and health of fish.
Understanding the Process: Mixing, Forming, Drying
The production process of fish feed involves several key stages, including mixing, forming, and drying, each of which plays a critical role in the quality and nutritional value of the final product.
Mixing is the initial stage of feed production, where raw ingredients are blended to create a homogeneous feed mixture. This process ensures that each pellet or extrudate contains the correct proportions of proteins, carbohydrates, fats, vitamins, and minerals essential for fish growth and health. Proper mixing is essential for achieving uniform feed quality and preventing nutrient imbalances that can adversely affect fish performance.
Forming is the next stage, where the mixed feed ingredients are shaped into pellets or extrudates suitable for consumption by fish. In pelletizing machines, the feed mixture is forced through a die and cut into uniform pellets of desired sizes. Extruders use a high-pressure extrusion process to form the feed mixture into expanded, floating pellets with precise densities and textures. The forming stage is critical for producing feed particles that meet the nutritional needs and feeding behaviors of target fish species.
Drying is the final stage of the feed production process, where moisture is removed from the formed pellets or extrudates to enhance shelf life and prevent microbial growth. Drying can be achieved through various methods, including air drying, fluidized bed drying, and belt drying, depending on the feed formulation and production capacity. Proper drying ensures that the feed pellets or extrudates have the appropriate moisture content for storage and transportation without compromising their nutritional quality.
Understanding the mixing, forming, and drying processes is essential for producing high-quality fish feed that meets the nutritional requirements of target fish species and supports their optimal growth and health. By optimizing each stage of the production process, aquafeed manufacturers can produce feed products that contribute to the sustainability and profitability of the aquaculture industry.
Quality Control Measures in Fish Food Machine Operations
Ensuring the quality of fish food machine operations is paramount in the aquaculture industry to produce safe and nutritious feed for aquatic species. Quality control measures are implemented throughout the production process to maintain high standards and meet regulatory requirements.
Firstly, strict adherence to standardized operating procedures (SOPs) is essential. These SOPs outline the steps involved in each stage of the production process, including ingredient handling, mixing, extrusion or pelletization, and packaging. By following established procedures consistently, operators can minimize variability and ensure the uniformity and quality of the final product.
Secondly, regular monitoring and testing of key parameters are conducted to verify product quality. This includes testing the moisture content, particle size distribution, and nutritional composition of the feed pellets or extrudates. Advanced analytical techniques, such as near-infrared spectroscopy (NIRS) and chromatography, are employed to assess the nutritional integrity and safety of the feed.
Furthermore, comprehensive record-keeping practices are implemented to track and trace the production process from raw material intake to finished product distribution. This includes documenting batch numbers, production dates, ingredient sources, and quality control test results. By maintaining detailed records, manufacturers can identify and address any deviations from established quality standards promptly.
Maintenance and Cleaning Protocols for Fish Food Machines
Regular maintenance and cleaning of fish food machines are essential to ensure their optimal performance, longevity, and hygiene. Proper maintenance protocols help prevent equipment breakdowns, minimize production downtime, and uphold food safety standards.
Scheduled maintenance tasks include routine inspection of machine components, lubrication of moving parts, and calibration of control systems. These tasks are performed according to manufacturer recommendations and industry best practices to prevent mechanical failures and ensure the reliability of the equipment.
Additionally, cleaning protocols are implemented to remove residues, contaminants, and microbial growth from the surfaces of fish food machines. This involves disassembling machine components, such as hoppers, conveyors, and dies, and cleaning them thoroughly with food-grade detergents and sanitizers. Special attention is paid to areas prone to product buildup, such as mixing chambers and extrusion screws, to prevent cross-contamination and maintain product quality.
Moreover, sanitation procedures are enforced to promote a hygienic production environment and prevent the spread of pathogens. This includes implementing Good Manufacturing Practices (GMPs), such as personnel hygiene protocols, facility sanitation schedules, and pest control measures. By adhering to stringent cleanliness standards, manufacturers can ensure the safety and integrity of the fish feed produced by their machines.
Compare manufacturers to help you choose a better machine
When considering fish food machine manufacturers like LOYAL and FEN, it's essential to evaluate various factors to make an informed decision. Below is a simple comparison table highlighting key aspects of both manufacturers:
Aspect |
LOYAL Company |
FEN Company |
Reputation |
Well-established with a strong track record of quality products and customer satisfaction. |
Relatively new in the market, with limited feedback and reviews. |
Product Range |
Offers a diverse range of fish food machines catering to different production scales and feed formulations. |
Focuses primarily on a specific type of fish food machine, potentially limiting options for customers. |
Technology and Innovation |
Incorporates cutting-edge technology and innovation to enhance product performance and efficiency. |
May lag behind in technological advancements, impacting machine capabilities and productivity. |
Customer Support |
Provides excellent customer support services, including timely assistance, maintenance, and troubleshooting. |
Customer support quality may vary, given the company's limited experience and resources. |
While both companies offer fish food machines, the choice ultimately depends on individual preferences, production requirements, and budget constraints. Prospective buyers are encouraged to conduct thorough research, request product demonstrations, and seek recommendations from industry experts or existing customers before making a decision.
Sustainability in Fish Food Machine Manufacturing
Sustainability has become a pressing concern in the manufacturing industry, including the production of fish food machines. Manufacturers like LOYAL and FEN are increasingly adopting sustainable practices to minimize their environmental impact and promote long-term viability.
One aspect of sustainability in fish food machine manufacturing is the use of eco-friendly materials and energy-efficient technologies. Companies prioritize the use of recyclable materials and employ energy-saving features in their machines to reduce resource consumption and carbon emissions during production and operation.
Additionally, sustainable manufacturing practices extend to waste management and disposal. Both LOYAL and FEN implement strategies to minimize waste generation in their production processes and responsibly manage any unavoidable waste through recycling or proper disposal methods.
Furthermore, sustainability initiatives often encompass the entire product lifecycle, including design, manufacturing, distribution, and end-of-life considerations. Manufacturers strive to optimize product design for durability, repairability, and recyclability, ensuring minimal environmental impact throughout the machine's lifespan.
In conclusion, sustainability is a critical consideration in fish food machine manufacturing, and companies like LOYAL and FEN are committed to integrating sustainable practices into their operations. By prioritizing eco-friendly materials, energy efficiency, waste management, and lifecycle considerations, these manufacturers contribute to the overall sustainability of the aquaculture industry while meeting the evolving needs of their customers.
Market Trends and Demand for Fish Food Machine Products
The market for fish food machine products is experiencing significant growth driven by various trends and factors influencing the demand for aquafeed worldwide. Understanding these market trends is crucial for manufacturers and stakeholders to capitalize on opportunities and meet evolving consumer needs.
One prominent trend in the fish food machine industry is the increasing demand for aquaculture products, driven by the growing global population and rising awareness of the health benefits of consuming fish. As a result, aquaculture operations are expanding, leading to higher demand for efficient and reliable fish food machines to produce quality feed for farmed fish.
Moreover, there is a growing preference for specialized feed formulations tailored to specific fish species and production goals. Fish farmers are increasingly seeking customized feed solutions that optimize growth, nutrition, and health while minimizing environmental impact. This trend has spurred innovation in fish food machine technology, with manufacturers developing equipment capable of producing a wide range of feed types, including pellets, extrudates, and flakes, to meet diverse customer demands.
Additionally, sustainability is emerging as a key consideration in the fish food machine market, driven by concerns over environmental impact and resource conservation. Manufacturers are increasingly incorporating sustainable practices into their operations, such as energy-efficient production processes, the use of eco-friendly materials, and waste reduction strategies. As sustainability becomes a priority for consumers and regulators alike, fish food machine products that align with these principles are expected to gain traction in the market.
Overall, the fish food machine market is characterized by increasing demand for specialized feed solutions, driven by the expansion of aquaculture and growing consumer preferences for sustainable products. Manufacturers that can innovate and adapt to these trends are well-positioned to capitalize on opportunities and maintain a competitive edge in the evolving market landscape.
Regulatory Compliance and Safety Standards in Fish Food Machine Industry
The fish food machine industry operates within a regulatory framework aimed at ensuring product safety, quality, and compliance with international standards. Regulatory bodies and industry organizations play a crucial role in establishing and enforcing regulations governing the design, manufacturing, and use of fish food machines to safeguard consumer health and promote industry transparency.
One of the primary regulatory considerations in the fish food machine industry is food safety. Manufacturers must adhere to strict hygiene and sanitation standards throughout the production process to prevent contamination and ensure the safety of the feed products. This includes implementing good manufacturing practices (GMP), sanitation protocols, and quality control measures to minimize the risk of microbial contamination and ensure product integrity.
Additionally, manufacturers are required to comply with industry-specific regulations and standards governing the design and operation of fish food machines. These standards address various aspects such as equipment design, materials used in construction, operational safety features, and performance specifications to ensure that machines meet industry requirements and operate safely and efficiently.
Furthermore, regulatory compliance extends to labeling and documentation requirements, where manufacturers must accurately label fish food machine products with essential information such as product specifications, usage instructions, and safety warnings. Compliance with labeling regulations ensures transparency and enables consumers to make informed purchasing decisions while reducing the risk of misuse or accidents.
Overall, regulatory compliance and safety standards are paramount in the fish food machine industry to uphold product quality, protect consumer health, and maintain industry credibility. Manufacturers must stay abreast of regulatory developments, invest in compliance efforts, and prioritize safety in all aspects of their operations to ensure market competitiveness and regulatory compliance.
References
1. Food and Agriculture Organization of the United Nations (FAO): https://www.fao.org/home/en/
2. American Society of Agricultural and Biological Engineers (ASABE): https://www.asabe.org/
3. The Aquaculture Engineering Society (AES): https://www.aesweb.org/
4. European Aquaculture Society (EAS): https://www.aquaeas.eu/
5. International Aquafeed Magazine:https://www.international-aquafeed.com/