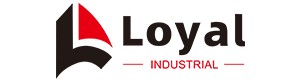
- Shandong Loyal Industrial Co.,Ltd.
- Macaroni Production Machine Instant Noodle Machine Biscuit Making Machine

Home> Company News> The Ultimate Protein Bar Production Line Guide to 2024

The Ultimate Protein Bar Production Line Guide to 2024
2024-07-01 16:06:15Introduction to Protein Bar Production Lines
Protein bars have become a staple in the health and fitness industry, driving demand for efficient and reliable Protein Bar Production Lines. These production lines are designed to handle the entire manufacturing process, from ingredient mixing to final packaging. Advanced production lines ensure consistent quality and high output, meeting the growing market needs.
A Protein Bar Production Line typically starts with the ingredient mixing phase. High-precision mixers ensure that all components, such as proteins, sweeteners, and binders, are blended uniformly. This step is crucial for achieving the desired texture and nutritional profile of the protein bars. Modern mixers come equipped with programmable settings, allowing for precise control over mixing times and speeds.
Following the mixing phase, the dough is transferred to forming machines. These machines shape the mixture into bars of uniform size and weight. Consistency in bar size is vital for packaging and consumer satisfaction. The forming machines in a Protein Bar Production Line are often automated, reducing manual labor and increasing production speed. Additionally, these machines can handle various bar shapes and sizes, offering flexibility to manufacturers.
The final steps in a Protein Bar Production Line involve cooling and packaging. Cooling tunnels are used to solidify the bars, ensuring they retain their shape during packaging. Packaging machines then wrap the bars in protective materials, readying them for distribution. Advanced packaging solutions often include features like vacuum sealing and modified atmosphere packaging, which extend the shelf life of the bars.
Benefits of Using Advanced Production Line Technology
Benefit |
Description |
Enhanced Efficiency |
Advanced Protein Bar Production Lines significantly boost efficiency. Automated processes reduce manual labor, leading to faster production rates and lower operational costs. High-speed machinery ensures that large quantities of protein bars can be produced in a shorter time frame. |
Consistency and Quality Control |
These production lines ensure uniformity in each batch, maintaining consistent quality. Automated systems precisely control ingredient ratios and mixing times, resulting in protein bars with consistent texture, flavor, and nutritional content. This reliability is crucial for brand reputation and consumer trust. |
Flexibility and Scalability |
Modern Protein Bar Production Lines offer flexibility to handle different bar recipes and formats. This adaptability allows manufacturers to quickly respond to market trends and introduce new products without extensive reconfiguration. Scalability ensures that production can be easily increased as demand grows. |
Hygiene and Safety Compliance |
Advanced production lines are designed with food safety in mind. They use food-grade materials and incorporate features that facilitate easy cleaning and maintenance. This ensures compliance with stringent hygiene standards, reducing the risk of contamination and ensuring the safety of the final product. |
Energy Efficiency and Sustainability |
Energy-efficient machinery reduces operational costs and minimizes environmental impact. These production lines often feature energy-saving technologies and optimized resource usage, contributing to sustainability goals. Investing in such technology also aligns with increasing consumer demand for eco-friendly practices. |
Reduced Downtime and Maintenance Costs |
High-quality machinery designed for durability requires less frequent maintenance. When maintenance is needed, advanced diagnostic tools and easy-to-replace components minimize downtime. This ensures continuous production and reduces the costs associated with machine repairs and production halts. |
Integration with Digital Technologies |
Modern Protein Bar Production Lines can integrate with digital technologies like IoT and AI. These integrations allow for real-time monitoring and data analysis, enhancing production efficiency and predictive maintenance. Manufacturers can optimize operations and quickly address issues, ensuring smooth production. |
Understanding the Automated Mixing Process
The automated mixing process is a fundamental aspect of the Protein Bar Production Line, ensuring that all ingredients are uniformly combined to create a consistent and high-quality product. Advanced mixing machines are designed to handle a variety of ingredients, including proteins, sweeteners, binders, and flavorings. These machines utilize precise control systems to manage the mixing speed, duration, and temperature, which are critical factors in achieving the desired texture and consistency.
One of the key benefits of an automated mixing process in a Protein Bar Production Line is the ability to maintain consistency across large batches. Automated systems minimize human error, ensuring that each batch is mixed according to the exact specifications. This consistency is crucial for meeting quality standards and ensuring that consumers receive a uniform product every time. The automated process also allows for better control over ingredient ratios, which is essential for nutritional accuracy.
Additionally, automated mixing machines are equipped with advanced features such as programmable settings and real-time monitoring. These features allow operators to set specific parameters for different recipes, making it easy to switch between product variations without extensive downtime. Real-time monitoring ensures that any deviations from the set parameters are immediately corrected, preventing potential issues before they affect the final product.
Furthermore, the automated mixing process enhances efficiency and reduces production time. By streamlining the mixing stage, manufacturers can increase their output and meet the growing demand for protein bars. The use of automated systems also reduces labor costs and minimizes the risk of contamination, as the process is enclosed and requires minimal human intervention. Overall, the automated mixing process is a critical component of a modern Protein Bar Production Line, contributing to improved quality, consistency, and efficiency.
Key Components of a Protein Bar Production Line
Component |
Description |
Automated Mixer |
Mixes ingredients uniformly with precise control over speed, duration, and temperature. |
Extruder |
Shapes the mixed dough into bars with consistent size and shape. |
Cooling Tunnel |
Cools the extruded bars to set their shape and improve texture. |
Cutting Machine |
Cuts the continuous bar into individual portions with high precision. |
Wrapper |
Wraps each bar individually to maintain freshness and hygiene. |
Metal Detector |
Ensures that no metal contaminants are present in the final product. |
Packaging Machine |
Packages multiple bars into boxes or other forms of collective packaging. |
Control System |
Manages and monitors the entire production process, ensuring all components work in sync. |
Cleaning System |
Automated cleaning mechanisms that ensure machinery is kept hygienic and ready for use. |
Inspection System |
Checks the quality of bars at various stages to ensure they meet predefined standards. |
Each component in the Protein Bar Production Line plays a crucial role in ensuring the efficiency and quality of the final product. The automated mixer starts the process by uniformly blending the ingredients, which is vital for achieving a consistent texture and taste. The extruder then shapes the mixture into bars, ensuring uniformity in size and shape, which is essential for packaging and consumer satisfaction.
The cooling tunnel is critical for setting the bars and improving their texture, making them ready for cutting. The cutting machine divides the continuous bar into individual portions with high precision, ensuring each bar meets the desired weight and size specifications. Wrappers and packaging machines then ensure that each bar is hygienically sealed and ready for distribution, maintaining the product's freshness and extending its shelf life.
Incorporating advanced control systems allows for real-time monitoring and adjustments, ensuring the entire Protein Bar Production Line operates smoothly and efficiently. Automated cleaning and inspection systems further enhance the production line's efficiency, ensuring that the machinery remains clean and that the final products meet high-quality standards. By integrating these components, manufacturers can produce protein bars that consistently meet consumer expectations and regulatory requirements.
Packaging Solutions for Protein Bars
Effective packaging solutions are crucial for the success of any Protein Bar Production Line. Packaging not only preserves the product's quality and extends its shelf life but also plays a significant role in branding and customer appeal. The latest advancements in packaging machinery offer a variety of options, from individual bar wrappers to multipack formats, ensuring versatility for different market needs.
A key aspect of packaging solutions in a Protein Bar Production Line is the use of automated systems. These systems ensure high-speed, precise packaging, reducing labor costs and minimizing human error. Automated packaging machines can handle various materials, including plastic, foil, and biodegradable wraps, catering to different sustainability goals. The integration of these systems with the production line ensures a seamless transition from manufacturing to packaging, maintaining the efficiency of the entire process.
Moreover, packaging solutions must focus on maintaining the integrity of the protein bars. This includes using materials that provide adequate barrier properties to protect against moisture, oxygen, and light. The choice of packaging material directly impacts the product's shelf life and quality. For instance, vacuum-sealed packaging is an excellent option for maintaining freshness and preventing spoilage, which is essential for protein bars containing sensitive ingredients.
Customization and branding are also vital components of packaging solutions. The Protein Bar Production Line should incorporate flexible packaging systems that allow for easy changes in design and labeling. This flexibility is crucial for marketing purposes, as it enables manufacturers to quickly adapt to new trends and consumer preferences. Additionally, eye-catching designs and informative labels can enhance the product's appeal, helping to attract and retain customers.
Maintenance Tips for Long-term Efficiency
Maintaining the efficiency and longevity of a Protein Bar Production Line requires regular and thorough maintenance practices. Proper maintenance ensures that the machinery operates at optimal performance, reducing the risk of unexpected breakdowns and costly downtime. Implementing a structured maintenance schedule is essential for the smooth functioning of the production line.
Routine inspections are a fundamental aspect of maintenance. Regularly checking for wear and tear, loose components, and potential malfunctions can help identify issues before they escalate. This proactive approach allows for timely repairs and replacements, ensuring the continuous operation of the Protein Bar Production Line. Additionally, keeping detailed records of maintenance activities can help track the performance and condition of the machinery over time.
Lubrication is another critical maintenance task that significantly impacts the machinery's efficiency. Proper lubrication reduces friction between moving parts, minimizing wear and extending the life of the equipment. It is essential to use the right type of lubricant recommended by the manufacturer and to apply it according to the specified intervals. Over-lubrication or under-lubrication can both cause damage to the machinery, so precision is key.
Training and empowering staff to perform basic maintenance tasks can also enhance the efficiency of the Protein Bar Production Line. Operators should be knowledgeable about the machinery they are handling and capable of performing routine checks and minor repairs. This not only reduces dependency on specialized maintenance personnel but also ensures that potential issues are addressed promptly, maintaining the production line's overall efficiency.
Emerging Trends in Protein Bar Manufacturing
The Protein Bar Production Line is evolving with the emergence of new trends and technologies that are shaping the future of the industry. One significant trend is the increasing demand for clean-label products. Consumers are becoming more health-conscious and prefer protein bars with simple, natural ingredients. This trend has led manufacturers to invest in machinery that can handle organic and minimally processed ingredients without compromising on quality or efficiency.
Sustainability is another crucial trend influencing the Protein Bar Production Line. Manufacturers are seeking eco-friendly production methods and packaging solutions to reduce their environmental footprint. This includes using energy-efficient machinery, sourcing sustainable raw materials, and adopting recyclable or biodegradable packaging. Implementing these practices not only meets consumer demand for greener products but also aligns with global sustainability goals.
Technological advancements are also driving innovation in protein bar manufacturing. The integration of IoT (Internet of Things) and AI (Artificial Intelligence) into the Protein Bar Production Line allows for real-time monitoring and optimization of the production process. Smart sensors and data analytics can detect inefficiencies, predict maintenance needs, and provide insights for continuous improvement. These technologies enhance productivity and ensure consistent product quality.
Customization and personalization are becoming increasingly important in the protein bar market. Consumers are looking for products tailored to their specific dietary needs and preferences. This trend has led to the development of flexible production lines that can quickly adapt to produce small batches of customized protein bars. Advanced machinery with modular designs and quick-change capabilities enables manufacturers to cater to this growing demand efficiently.
Future Outlook: Innovations and Challenges
The future of the Protein Bar Production Line is poised for exciting innovations and developments. One of the key areas of focus will be the integration of advanced automation and robotics. These technologies will enhance precision, speed, and consistency in the production process, reducing labor costs and minimizing human error. Automated systems will handle everything from ingredient mixing to packaging, streamlining the entire production line.
Innovation in ingredient processing is another area that will see significant advancements. As the demand for high-protein, low-sugar, and allergen-free bars continues to grow, manufacturers will need to invest in machinery capable of handling a diverse range of ingredients. This includes advanced mixing and blending machines that ensure uniformity and quality, even with complex ingredient combinations.
Despite the exciting innovations, the Protein Bar Production Line will face several challenges. One of the primary challenges will be maintaining product quality and safety while scaling up production. As manufacturers expand their operations to meet growing demand, ensuring that the quality of each bar remains consistent will be crucial. This will require continuous investment in high-quality machinery and rigorous quality control processes.
Regulatory compliance will also pose challenges for the Protein Bar Production Line. As global food safety standards become more stringent, manufacturers must ensure their production processes meet all regulatory requirements. This includes adhering to hygiene standards, proper labeling, and ensuring traceability throughout the supply chain. Staying updated with the latest regulations and investing in compliant machinery will be essential to navigate these challenges.
In conclusion, the Protein Bar Production Line is set for significant advancements, driven by trends in consumer preferences, technological innovations, and sustainability goals. By embracing these trends and addressing the associated challenges, manufacturers can ensure they remain competitive and meet the evolving demands of the protein bar market.
Reference
The following are five authoritative foreign literature websites in the field of Industrial food machinery:
1. Food Engineering Magazine
Website: https://www.foodengineeringmag.com/
2.Food Processing Magazine
Website: https://www.foodprocessing.com/
3.Journal of Food Engineering
Website:https://www.journals.elsevier.com/journal-of-food-engineering
4. Food Manufacturing Magazine
Website:https://www.foodmanufacturing.com/
5. International Journal of Food Science & Technology
Website:https://onlinelibrary.wiley.com/