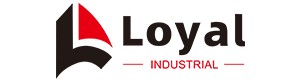
- Shandong Loyal Industrial Co.,Ltd.
- Macaroni Production Machine Instant Noodle Machine Biscuit Making Machine

Home> Company News> How To Choose The Best Dog Food Process Line: 2024 Buyer’s Guide

How To Choose The Best Dog Food Process Line: 2024 Buyer’s Guide
2024-10-18 09:40:59Overview of Automated Dog Food Process Lines
The dog food industry has seen significant advancements in manufacturing processes, particularly with the integration of automated dog food process lines. An automated dog food process line refers to a series of interconnected machines and equipment that handle the entire production cycle of dog food, from raw ingredient handling to final packaging. This modern manufacturing approach has revolutionized the way dog food is produced, ensuring efficiency, consistency, and safety in every stage of the process.
Automated dog food process lines are designed to streamline production, minimize human error, and optimize resource utilization. These systems typically incorporate state-of-the-art technology and sophisticated software that allows for precise control over every aspect of the manufacturing process. From mixing and extruding raw ingredients to drying, cooling, and packaging the finished product, automated dog food process lines ensure that every batch meets the highest quality standards.
One of the key benefits of automated dog food process lines is their ability to handle large volumes of production with minimal downtime. This is particularly important in the dog food industry, where demand can fluctuate rapidly and manufacturers need to be able to scale their production accordingly. Automated systems are also more consistent in terms of product quality, as they eliminate the variability that can be introduced by manual processes.
Moreover, automated dog food process lines are designed with safety and hygiene in mind. They incorporate features such as enclosed machinery, easy-to-clean surfaces, and advanced sanitation systems to ensure that the production environment is free from contamination. This is crucial for maintaining the safety and integrity of the final product, as well as protecting the health of the workers involved in the production process.
In summary, automated dog food process lines represent a significant leap forward in modern manufacturing for the dog food industry. By incorporating advanced technology and sophisticated software, these systems enable manufacturers to produce high-quality dog food in a consistent, efficient, and safe manner. As the industry continues to evolve, it is likely that automated dog food process lines will become even more sophisticated and integrated into the overall manufacturing process.
Components and Functionality of Automated Dog Food Process Lines
Automated dog food process lines are composed of several key components that work together to ensure the efficient and effective production of dog food. Each component serves a specific function and contributes to the overall quality and consistency of the final product.
One of the first components in an automated dog food process line is the ingredient handling system. This system is responsible for receiving, storing, and delivering raw ingredients to the mixing stage. It typically includes conveyors, hoppers, and weighing scales that ensure the correct quantities of each ingredient are delivered to the mixer. The ingredient handling system is designed to minimize waste and ensure that raw materials are handled in a safe and hygienic manner.
The mixing stage is where raw ingredients are combined to form the dog food formula. Automated mixing systems use high-shear mixers or paddle mixers to blend the ingredients evenly. These mixers are equipped with sensors that monitor the mixing process and ensure that the ingredients are thoroughly combined. The mixing stage is crucial for achieving a consistent texture and nutritional profile in the final product.
Once the ingredients are mixed, they are fed into an extruder. The extruder is a key component in the automated dog food process line, as it shapes and cooks the raw mixture into the desired form. Extruders come in various sizes and configurations, depending on the type of dog food being produced. They use heat and pressure to force the mixture through a die, which shapes the dog food into kibbles or other forms. The extruder also controls the texture and density of the final product.
After the extrusion process, the dog food is conveyed to a drying and cooling system. This system removes excess moisture from the dog food and cools it to the desired temperature. Drying and cooling are essential steps in the production process, as they ensure that the dog food is stable and has a long shelf life.
Finally, the dog food is conveyed to the packaging and labeling system. This system automatically fills bags or containers with the finished product, applies labels with product information, and seals the packages. Automated packaging systems are designed to minimize human error and ensure that each package meets the required quality standards.
In conclusion, automated dog food process lines are composed of several key components that work together to ensure the efficient and effective production of dog food. From ingredient handling to mixing, extrusion, drying, cooling, and packaging, each component serves a specific function and contributes to the overall quality and consistency of the final product. As technology continues to advance, it is likely that these components will become even more sophisticated and integrated into the overall manufacturing process.
Advantages and Disadvantages of Automated Dog Food Process Lines
Automated dog food process lines offer numerous advantages over traditional manual production methods, but they also come with some disadvantages. Understanding both the pros and cons can help manufacturers make informed decisions about whether to invest in automation.
Advantages:
Increased Efficiency: Automated dog food process lines are designed to maximize production capacity while minimizing downtime. This results in faster production speeds and higher output levels, allowing manufacturers to meet customer demand more effectively.
Consistency in Quality: Automated systems use precision machinery and sensors to ensure that each batch of dog food is produced to the same high standards. This consistency in quality is essential for maintaining customer satisfaction and loyalty.
Reduced Labor Costs: Automating the production process reduces the need for manual labor, which can lead to significant cost savings. Automated systems also minimize the risk of human error, which can further reduce waste and increase productivity.
Enhanced Safety: Automated dog food process lines incorporate safety features that protect workers from potential hazards, such as moving machinery and hazardous materials. This reduces the risk of workplace accidents and injuries.
Scalability: Automated systems can be easily scaled up or down to meet changing production needs. This flexibility allows manufacturers to adapt to market trends and customer preferences without significant investments in new equipment.
Disadvantages:
High Initial Investment: The upfront cost of purchasing and installing automated dog food process lines can be significant. This can be a barrier to entry for smaller manufacturers or those with limited budgets.
Technical Expertise Required: Operating and maintaining automated systems requires a high level of technical expertise. Manufacturers may need to hire or train additional staff to manage these systems effectively.
Dependency on Technology: Automated systems can be susceptible to technical failures or breakdowns. This can lead to production delays and potential losses if not properly managed.
Limited Customization: Automated dog food process lines are typically designed for mass production, which may limit the ability to customize products for specific customer needs or preferences.
Environmental Impact: While automated systems can reduce waste and improve efficiency, they may also have an environmental impact, such as increased energy consumption and waste generation. Manufacturers should consider their overall environmental footprint when investing in automation.
In conclusion, automated dog food process lines offer numerous advantages, including increased efficiency, consistency in quality, reduced labor costs, enhanced safety, and scalability. However, they also come with some disadvantages, such as high initial investment, technical expertise required, dependency on technology, limited customization, and environmental impact. Manufacturers should carefully weigh these pros and cons before making a decision about whether to invest in automation.
Challenges and Solutions in Automated Dog Food Process Lines
Despite the numerous advantages of automated dog food process lines, they do come with their own set of challenges. Addressing these challenges effectively is crucial for maintaining optimal production efficiency and ensuring product quality.
One major challenge is the complexity of the machinery involved. Automated systems often incorporate sophisticated technology and precision engineering, which requires a high level of expertise for maintenance and troubleshooting. To overcome this, manufacturers must invest in training their workforce to handle these advanced systems competently. Regular training sessions and workshops can help keep employees updated with the latest technological advancements and best practices in automation.
Another challenge is the need for flexibility in production. Dog food manufacturers often need to produce a wide variety of products to cater to different consumer preferences and dietary requirements. Automated systems must be designed to accommodate quick and easy changes in recipes and production parameters. This can be achieved through the use of modular and customizable machinery that allows for easy adjustments and upgrades.
Moreover, maintaining hygiene and safety standards in automated process lines is paramount. Dog food production involves handling raw materials that can be susceptible to contamination. Therefore, manufacturers must implement stringent cleaning and sanitation protocols to ensure that automated systems remain free from harmful microorganisms. Advanced cleaning technologies, such as high-pressure water jets and steam cleaning systems, can be incorporated into the process line to facilitate efficient and thorough cleaning.
Furthermore, the integration of automation with existing manual processes can pose a challenge. Manufacturers must carefully plan and execute the transition to automation to minimize disruptions in production and maintain a smooth workflow. This often involves a phased approach, where certain aspects of the production process are automated first, while others are gradually integrated over time.
In conclusion, while automated dog food process lines offer significant advantages, they do come with their own set of challenges. By investing in training, designing flexible machinery, maintaining hygiene standards, and carefully planning the transition to automation, manufacturers can overcome these challenges and harness the full potential of automated systems to drive efficiency, quality, and innovation in dog food production.
Future Trends and Innovations in Automated Dog Food Process Lines
The dog food industry is constantly evolving, driven by consumer demands for healthier, more sustainable, and personalized products. Automated dog food process lines are at the forefront of this evolution, incorporating cutting-edge technology to meet these demands and drive innovation in manufacturing.
One significant future trend is the integration of artificial intelligence (AI) and machine learning algorithms into automated process lines. These technologies enable manufacturers to optimize production processes in real-time, reducing waste, improving quality, and enhancing productivity. For example, AI-driven predictive maintenance systems can predict machinery failures before they occur, allowing for timely repairs and minimizing downtime.
Another trend is the increasing use of robotics in dog food production. Advanced robotic systems can handle delicate tasks, such as precise ingredient measurement and formulation, with unmatched accuracy and efficiency. These robots can also work in harsh environments, such as those with high temperatures or exposure to hazardous materials, ensuring the safety of human workers.
Sustainability is also a key focus area for the dog food industry. Automated process lines are being designed to minimize environmental impact through the use of energy-efficient machinery, recyclable packaging materials, and waste reduction technologies. For instance, manufacturers are incorporating closed-loop water recycling systems that reuse water from production processes, reducing water consumption and waste.
Consumer preferences for personalized dog food products are also driving innovation in automation. Automated systems are being developed to create customized formulas based on individual dogs' dietary needs, age, breed, and activity levels. This personalized approach not only enhances the nutritional value of the products but also strengthens consumer loyalty and satisfaction.
Furthermore, the rise of the Internet of Things (IoT) is transforming the way automated dog food process lines operate. IoT-enabled devices can collect and analyze vast amounts of data from production processes, providing manufacturers with actionable insights to improve efficiency, quality, and safety. This data-driven approach to manufacturing allows for more informed decision-making and continuous improvement.
In conclusion, the future of automated dog food process lines is bright, with exciting trends and innovations shaping the industry. By embracing cutting-edge technologies such as AI, robotics, sustainability practices, personalized product formulation, and IoT, manufacturers can stay ahead of the curve and meet the evolving needs of consumers. These advancements will not only enhance the efficiency and quality of dog food production but also contribute to a more sustainable and innovative manufacturing landscape.
Reference
The following are five authoritative foreign literature websites in the field of Industrial food machinery:
1. Food Engineering Magazine
Website: https://www.foodengineeringmag.com/
2.Food Processing Magazine
Website: https://www.foodprocessing.com/
3.Journal of Food Engineering
Website:https://www.journals.elsevier.com/journal-of-food-engineering
4. Food Manufacturing Magazine
Website:https://www.foodmanufacturing.com/
5. International Journal of Food Science & Technology
Website:https://onlinelibrary.wiley.com/